Master the Global Market for Pencil Vending Machines: Key
Guide to Pencil Vending Machine
- Introduction: Navigating the Global Market for pencil vending machine
- Understanding pencil vending machine Types and Variations
- Key Industrial Applications of pencil vending machine
- Strategic Material Selection Guide for pencil vending machine
- In-depth Look: Manufacturing Processes and Quality Assurance for pencil vending machine
- Comprehensive Cost and Pricing Analysis for pencil vending machine Sourcing
- Spotlight on Potential pencil vending machine Manufacturers and Suppliers
- Essential Technical Properties and Trade Terminology for pencil vending machine
- Navigating Market Dynamics, Sourcing Trends, and Sustainability in the pencil vending machine Sector
- Frequently Asked Questions (FAQs) for B2B Buyers of pencil vending machine
- Strategic Sourcing Conclusion and Outlook for pencil vending machine
Introduction: Navigating the Global Market for pencil vending machine
In the evolving landscape of educational and office supplies, pencil vending machines have emerged as a practical solution to meet the diverse needs of consumers across various sectors. These automated dispensers not only enhance accessibility to essential writing instruments but also serve as a lucrative investment for businesses looking to tap into the growing demand for convenience and efficiency. For international B2B buyers, particularly from regions like Africa, South America, the Middle East, and Europe, understanding the intricacies of the pencil vending machine market is critical for making informed sourcing decisions.
This comprehensive guide delves into the various types of pencil vending machines available, examining their materials and manufacturing processes, as well as the quality control measures that ensure durability and reliability. Buyers will gain insights into leading suppliers, enabling them to identify trustworthy partners that align with their operational needs. Additionally, we explore pricing structures, market trends, and the competitive landscape, providing a holistic view of the industry.
Equipped with this knowledge, B2B buyers will be empowered to navigate the global market effectively, making strategic choices that enhance their procurement strategies. Whether you are looking to establish a new vending operation or expand an existing one, this guide offers the essential information you need to succeed in the dynamic world of pencil vending machines.
Understanding pencil vending machine Types and Variations
Type Name | Key Distinguishing Features | Primary B2B Applications | Brief Pros & Cons for Buyers |
---|---|---|---|
Traditional Mechanical | Manual operation with a coin slot and rotating mechanism | Schools, offices, and public spaces | Pros: Low maintenance, easy to use. Cons: Limited product variety, slower sales. |
Digital Touchscreen | Interactive screen, customizable product selection | Retail environments, exhibitions | Pros: Engaging user interface, data collection capabilities. Cons: Higher initial cost, requires power supply. |
Mobile Pencil Vending | Compact, portable design with limited stock | Events, trade shows, pop-up shops | Pros: Flexibility in location, quick setup. Cons: Smaller inventory, may require frequent restocking. |
Smart Inventory System | IoT-enabled for real-time inventory tracking | Large organizations, educational institutions | Pros: Efficient inventory management, reduces stockouts. Cons: Complexity in setup, potential technical issues. |
Eco-friendly Vending | Uses sustainable materials and offers eco-friendly products | Green initiatives, schools, and offices | Pros: Appeals to environmentally conscious consumers, supports sustainability goals. Cons: May have higher upfront costs, limited product options. |
Traditional Mechanical Vending Machines
Traditional mechanical pencil vending machines operate through a simple coin slot and a manual rotating mechanism. They are ideal for environments such as schools and offices where basic stationery supplies are needed. B2B buyers should consider their low maintenance requirements and ease of use, making them an attractive option for budget-conscious organizations. However, the limited product variety and slower sales potential can be drawbacks, particularly in high-traffic areas.
Digital Touchscreen Vending Machines
Digital touchscreen vending machines offer an interactive user experience, allowing customers to select products through a customizable interface. These machines are particularly well-suited for retail environments and exhibitions, where engaging customers is critical. B2B buyers should note the potential for data collection and analytics that can inform inventory decisions. The higher initial investment and reliance on power supply may pose challenges, particularly in remote locations.
Mobile Pencil Vending Machines
Mobile pencil vending machines are designed for portability, making them perfect for events, trade shows, and pop-up shops. Their compact size allows for easy transportation and quick setup, appealing to businesses that require flexibility. B2B buyers should weigh the benefits of mobility against the potential downsides, such as smaller inventory capacity and the need for frequent restocking. This type of machine is ideal for short-term use or dynamic sales environments.
Smart Inventory System Vending Machines
Smart inventory system vending machines leverage IoT technology to provide real-time inventory tracking and management. These machines are particularly beneficial for large organizations and educational institutions that require efficient stock management. B2B buyers should consider the advantages of reducing stockouts and enhancing operational efficiency. However, the complexity of setup and potential technical issues may require additional resources and expertise.
Eco-friendly Vending Machines
Eco-friendly vending machines focus on sustainability by utilizing environmentally friendly materials and offering eco-conscious products. They are increasingly popular among organizations committed to green initiatives, such as schools and offices looking to promote sustainability. B2B buyers should recognize the appeal of these machines to environmentally conscious consumers, though they may face higher upfront costs and a limited range of product options. Investing in eco-friendly solutions can enhance brand reputation and align with corporate social responsibility goals.
Related Video: Machine Learning in 2024 – Beginner’s Course
Key Industrial Applications of pencil vending machine
Industry/Sector | Specific Application of pencil vending machine | Value/Benefit for the Business | Key Sourcing Considerations for this Application |
---|---|---|---|
Education | School and University Supply Stations | Enhances accessibility to stationery, reduces waste | Durability, ease of use, payment systems compatibility |
Office and Corporate | Break Room and Meeting Room Supplies | Promotes a culture of preparedness and efficiency | Compact design, refill frequency, branding options |
Retail | Convenience Store or Shopping Mall Kiosks | Increases impulse purchases, attracts foot traffic | Location analysis, product variety, security features |
Event Management | Conferences and Trade Shows | Provides instant access to writing tools for attendees | Mobility, setup time, stock management capabilities |
Creative Industries | Art Studios and Design Firms | Supplies artists with immediate access to tools | Customization options, material quality, size variations |
Education
In educational institutions, pencil vending machines serve as vital supply stations, providing students with easy access to essential stationery. These machines can be strategically placed in high-traffic areas like hallways or libraries. The primary challenge they address is the frequent loss or misplacement of writing instruments, ensuring that students are always equipped for their studies. For international buyers, particularly in regions like Africa and South America, considerations such as durability and the ability to withstand high usage rates are critical. Additionally, systems that accept various payment methods, including mobile payments, can enhance usability.
Office and Corporate
Within corporate environments, pencil vending machines can be installed in break rooms or meeting areas to ensure that employees have immediate access to writing tools. This not only fosters a culture of preparedness but also increases overall office efficiency. International buyers should focus on compact designs that fit into limited space and consider how often the machines will need to be refilled. Custom branding options can also be beneficial for companies looking to enhance their corporate image.
Retail
In the retail sector, pencil vending machines can be utilized in convenience stores or shopping malls to increase impulse purchases. By positioning these machines at strategic locations, businesses can attract foot traffic and cater to customers who may need writing instruments on-the-go. Key sourcing considerations for retail applications include conducting a thorough location analysis to determine the best spots for installation, as well as ensuring that the machines are equipped with security features to prevent theft.
Event Management
At conferences and trade shows, pencil vending machines provide attendees with immediate access to writing tools, enhancing their experience and ensuring they can take notes or fill out forms without delay. The mobility of these machines is crucial, as they need to be easily transportable and quick to set up in various locations. Buyers should consider stock management capabilities to ensure that the machines are adequately supplied throughout the event, as well as the setup time required for efficient operation.
Creative Industries
For art studios and design firms, pencil vending machines can offer artists immediate access to various writing and drawing tools, thereby facilitating creativity and productivity. These machines can be customized to include a range of materials that cater to specific artistic needs. Buyers in this sector should prioritize customization options, material quality, and size variations to meet the diverse requirements of their clientele. Ensuring that the machines can handle different types of pencils and art supplies will also be essential for success in this market.
Related Video: DIY Vending Machine – Arduino based Mechatronics Project
Strategic Material Selection Guide for pencil vending machine
When selecting materials for pencil vending machines, international B2B buyers must consider various factors that impact performance, cost, and compatibility with specific markets. Below is an analysis of four common materials used in the construction of these machines, focusing on their properties, advantages, disadvantages, and specific considerations for buyers from Africa, South America, the Middle East, and Europe.
1. Stainless Steel
Key Properties:
Stainless steel is renowned for its excellent corrosion resistance, high strength, and ability to withstand a wide range of temperatures. It typically has a temperature rating of up to 800°C and can handle pressures exceeding 200 psi, making it suitable for various environments.
Pros & Cons:
The durability of stainless steel ensures a long lifespan, which is crucial for vending machines exposed to outdoor elements. However, it tends to be more expensive than other materials, leading to higher initial costs. Manufacturing complexity can also increase due to the need for specialized tools and processes.
Impact on Application:
Stainless steel is compatible with a variety of media, including water and air, making it versatile for different vending machine designs.
Considerations for International Buyers:
Compliance with international standards such as ASTM and DIN is essential. Buyers should also consider local regulations regarding food safety and hygiene, particularly in regions like the Middle East and Europe.
2. Mild Steel
Key Properties:
Mild steel is characterized by its malleability and ductility, with a typical yield strength of around 250 MPa. It is suitable for moderate temperature applications and can be treated for corrosion resistance.
Pros & Cons:
The primary advantage of mild steel is its low cost, making it an attractive option for budget-conscious buyers. However, its susceptibility to rust and corrosion limits its use in outdoor settings unless adequately treated, which can add to manufacturing costs.
Impact on Application:
Mild steel is best suited for indoor vending machines or environments with controlled conditions. It is not ideal for regions with high humidity or exposure to corrosive elements.
Considerations for International Buyers:
Buyers should ensure that any coatings or treatments applied to mild steel comply with local environmental regulations, particularly in South America and Africa, where regulations may vary significantly.
3. Aluminum
Key Properties:
Aluminum is lightweight yet strong, with excellent corrosion resistance. It can withstand temperatures up to 600°C and is often used in applications requiring lightweight materials.
Pros & Cons:
The lightweight nature of aluminum makes it easy to transport and install, reducing overall logistics costs. However, it is generally more expensive than mild steel and may not provide the same structural integrity under heavy loads.
Impact on Application:
Aluminum is suitable for vending machines that require portability or are installed in areas where weight is a concern. Its corrosion resistance makes it ideal for humid environments.
Considerations for International Buyers:
Aluminum products must adhere to specific standards, such as JIS in Japan or EN in Europe. Buyers from regions like Africa and the Middle East should verify the availability of aluminum grades that meet local requirements.
4. Plastic (Polycarbonate or ABS)
Key Properties:
Plastics like polycarbonate and ABS offer good impact resistance and can operate within a temperature range of -40°C to 120°C. They are lightweight and can be molded into complex shapes.
Pros & Cons:
Plastic materials are cost-effective and can be produced in various colors and designs, making them appealing for branding. However, they may not be as durable as metals and can degrade over time, especially under UV exposure.
Impact on Application:
Plastic is ideal for vending machines located indoors or in controlled environments. It is less suitable for outdoor applications unless specifically treated for UV and weather resistance.
Considerations for International Buyers:
Buyers should ensure that plastic materials comply with local safety standards, especially in Europe, where regulations regarding material safety are stringent.
Summary Table
Material | Typical Use Case for pencil vending machine | Key Advantage | Key Disadvantage/Limitation | Relative Cost (Low/Med/High) |
---|---|---|---|---|
Stainless Steel | Outdoor and high-durability applications | Excellent corrosion resistance | Higher initial cost | High |
Mild Steel | Indoor applications with controlled conditions | Cost-effective | Susceptible to rust | Low |
Aluminum | Portable and lightweight vending machines | Lightweight and corrosion-resistant | Higher cost than mild steel | Medium |
Plastic (Polycarbonate/ABS) | Indoor and decorative vending machines | Cost-effective and customizable | Less durable under UV exposure | Low |
This guide provides a foundational understanding of material selection for pencil vending machines, enabling international B2B buyers to make informed decisions based on their specific needs and market conditions.
In-depth Look: Manufacturing Processes and Quality Assurance for pencil vending machine
Manufacturing Processes for Pencil Vending Machines
The manufacturing of pencil vending machines involves a series of well-defined stages, each critical to ensuring the final product meets quality and functionality standards. Understanding these processes is essential for B2B buyers seeking to make informed purchasing decisions.
1. Material Preparation
The first stage involves selecting appropriate materials that can withstand the rigors of everyday use. Common materials include:
- Metal Components: Typically steel or aluminum for structural integrity.
- Plastic Parts: High-density polyethylene (HDPE) or polycarbonate for durability and aesthetic appeal.
- Electronic Components: Circuit boards and sensors that require materials like FR-4 for reliability.
Buyers should ensure that suppliers adhere to material specifications, as the choice of materials directly affects the machine’s lifespan and performance.
2. Forming
Once materials are prepared, the next step is forming. This involves shaping the components through various techniques:
- Stamping: Used for creating metal parts, ensuring precise dimensions and reducing waste.
- Injection Molding: Essential for producing plastic components, allowing for complex shapes and high-volume production.
- CNC Machining: Employed for custom or precision parts, ensuring that even intricate designs are accurately manufactured.
Buyers should inquire about the specific forming techniques used and their implications on the cost and lead time of the machines.
3. Assembly
Assembly is a crucial stage where individual components come together. This process can be manual or automated, depending on the complexity and volume of production. Key aspects include:
- Integration of Mechanical and Electronic Systems: Ensuring that the vending mechanism, payment systems, and sensors work seamlessly together.
- Quality Checks During Assembly: Continuous monitoring to catch defects early, enhancing overall quality.
B2B buyers should assess the supplier’s assembly capabilities, including workforce training and the use of automation technologies, to ensure efficiency and quality.
4. Finishing
The final stage involves finishing processes that enhance the machine’s appearance and functionality. This includes:
- Painting and Coating: To protect against corrosion and wear, as well as to provide an appealing aesthetic.
- Quality Inspections: Conducting visual and functional tests to ensure the machine meets all specifications.
Buyers should consider suppliers who offer customization options in finishing to align with branding requirements.
Quality Assurance for Pencil Vending Machines
Quality assurance (QA) is paramount in the manufacturing of pencil vending machines, ensuring that products meet international standards and customer expectations. Implementing robust QA processes helps mitigate risks associated with defects and recalls.
Relevant International Standards
For international B2B buyers, understanding the relevant quality standards is crucial. Key certifications to look for include:
- ISO 9001: A global standard for quality management systems that ensures consistent quality across processes.
- CE Marking: Indicates conformity with health, safety, and environmental protection standards for products sold within the European Economic Area.
- API Standards: Particularly for electronic components, ensuring reliability and safety.
Buyers should request documentation proving compliance with these standards, as they reflect a supplier’s commitment to quality.
Quality Control Checkpoints
Quality control (QC) checkpoints are integral to the manufacturing process. Common checkpoints include:
- Incoming Quality Control (IQC): Inspecting raw materials upon arrival to ensure they meet specifications.
- In-Process Quality Control (IPQC): Continuous monitoring during production to identify defects in real-time.
- Final Quality Control (FQC): Comprehensive testing of the finished product to verify performance and compliance with specifications.
Establishing clear expectations regarding QC checkpoints can help buyers ensure that their suppliers maintain high standards throughout the production process.
Common Testing Methods
Various testing methods are employed to validate the quality of pencil vending machines, including:
- Functional Testing: Ensuring that the vending mechanism operates correctly under different conditions.
- Durability Testing: Simulating prolonged use to assess wear and tear.
- Safety Testing: Evaluating electrical components to prevent hazards.
Buyers should inquire about the specific testing methods used and their effectiveness in identifying potential issues.
Verifying Supplier Quality Control
To ensure that suppliers maintain rigorous quality control, B2B buyers should consider the following strategies:
- Conducting Audits: Regular on-site audits can provide insights into the supplier’s manufacturing processes and QC practices.
- Requesting QC Reports: Suppliers should provide detailed reports of their QC activities, including inspection results and corrective actions taken.
- Engaging Third-Party Inspectors: Utilizing independent inspectors can provide an unbiased evaluation of the supplier’s quality assurance practices.
Buyers from diverse regions, including Africa, South America, the Middle East, and Europe, should be particularly vigilant in verifying these practices, as differing regulations and standards can impact product quality.
Quality Control and Certification Nuances
For international buyers, understanding the nuances of QC and certification is vital. Each region may have specific regulatory requirements that affect product compliance. Here are some insights:
- Regional Certifications: Buyers should familiarize themselves with local certifications in their respective markets, such as ANATEL in Brazil or GOST in Russia.
- Cultural Considerations: Different regions may have varying perceptions of quality and safety standards, which can influence supplier selection.
- Supply Chain Transparency: Engaging suppliers who prioritize transparency in their operations can help mitigate risks associated with quality and compliance.
By focusing on these areas, B2B buyers can navigate the complexities of manufacturing processes and quality assurance effectively, ensuring that they procure reliable and high-quality pencil vending machines.
Related Video: How Pens Are Made In Factory | Pen Manufacturing Industry | Ball Pen Production
Comprehensive Cost and Pricing Analysis for pencil vending machine Sourcing
Understanding the Cost Structure of Pencil Vending Machines
When considering the sourcing of pencil vending machines, it is crucial to have a clear understanding of the cost components involved. This will enable international B2B buyers to make informed decisions and negotiate effectively.
Cost Components:
-
Materials: The primary components of a pencil vending machine include metal, plastic, and electronic parts. The quality and sourcing of these materials can significantly influence the overall cost. For instance, higher-grade materials may offer durability but can also increase the base price.
-
Labor: Labor costs vary widely depending on the country of manufacture. Regions with lower labor costs, such as parts of Asia, may provide significant savings. However, it is essential to consider the skill level of the workforce, as this impacts production quality and efficiency.
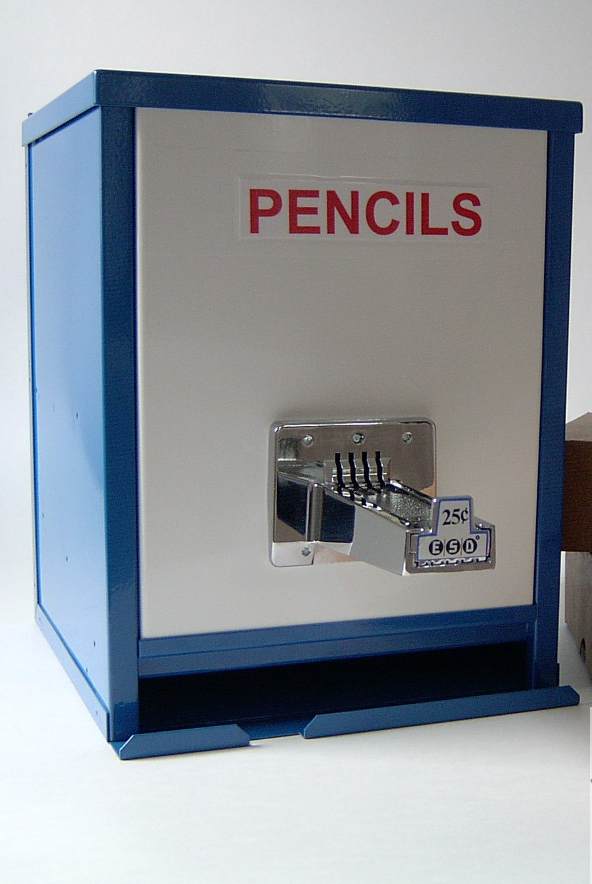
Illustrative Image (Source: Google Search)
-
Manufacturing Overhead: This encompasses the indirect costs associated with production, such as utilities and facility maintenance. Buyers should inquire about how these costs are allocated to the pricing structure.
-
Tooling: If customization or specific specifications are required, tooling costs can be a significant factor. Custom tooling may require a higher initial investment, but it can lead to better-fit products.
-
Quality Control (QC): Ensuring the quality of the machines is vital. Implementing robust QC processes can increase costs but will enhance product reliability and reduce long-term maintenance issues.
-
Logistics: Shipping costs, including freight, insurance, and customs duties, can dramatically affect the final price. These costs vary based on the origin of the machine, destination country, and chosen shipping method.
-
Margin: Suppliers will typically add a profit margin to cover their expenses and risks. Understanding the market rate for this margin can help buyers negotiate better pricing.
Factors Influencing Pricing
Several factors influence the pricing of pencil vending machines, which buyers should consider:
-
Volume/MOQ (Minimum Order Quantity): Higher order volumes often lead to reduced unit prices. Buyers should assess their needs carefully to leverage bulk purchasing advantages.
-
Specifications/Customization: Customized machines tailored to specific needs may come at a premium. Understanding the trade-off between standard vs. custom models is essential.
-
Materials and Quality Certifications: Machines built with certified materials (e.g., environmental or safety standards) may incur higher costs but could also enhance the product’s marketability.
-
Supplier Factors: Reputation, reliability, and service level of the supplier can influence pricing. A supplier with a proven track record may justify higher prices due to perceived lower risk.
-
Incoterms: The chosen Incoterms (International Commercial Terms) determine the responsibilities of buyers and sellers in shipping and logistics. Understanding these can help avoid unexpected costs.
Buyer Tips for Cost-Efficiency
-
Negotiate Effectively: Establish clear communication with suppliers regarding pricing breakdowns. Leverage your understanding of cost components to negotiate more favorable terms.
-
Assess Total Cost of Ownership (TCO): Beyond the initial purchase price, consider maintenance, operational costs, and potential downtime. This holistic view can lead to better decision-making.
-
Understand Pricing Nuances: Different regions may have varying pricing strategies. For example, suppliers in Africa and South America may offer lower prices due to lower labor costs, but quality and service levels must be evaluated.
-
Conduct Market Research: Stay informed about industry trends and competitor pricing. This knowledge can empower you during negotiations and sourcing decisions.
-
Consider Local Partnerships: Collaborating with local distributors or agents can reduce logistics costs and streamline communication, ultimately affecting the overall cost structure.
Disclaimer on Pricing
Prices for pencil vending machines can vary significantly based on multiple factors, including but not limited to supplier, region, and market conditions. It is advisable for buyers to conduct thorough due diligence and obtain multiple quotes to ensure competitive pricing.
Spotlight on Potential pencil vending machine Manufacturers and Suppliers
- (No specific manufacturer data was available or requested for detailed profiling in this section for pencil vending machine.)*
Essential Technical Properties and Trade Terminology for pencil vending machine
Key Technical Properties of Pencil Vending Machines
When considering the purchase of pencil vending machines, understanding their technical specifications is crucial for making informed decisions. Here are some essential properties to evaluate:
-
Material Grade
The material used in the construction of the vending machine can significantly affect its durability and performance. Common materials include stainless steel and high-grade plastics. Stainless steel offers resistance to corrosion and wear, making it suitable for high-traffic environments. Choosing the right material is essential for ensuring longevity and reducing maintenance costs. -
Capacity
This specification refers to the number of pencils or related supplies the machine can hold. A higher capacity means fewer refills, which can be critical in high-demand locations like schools or office buildings. Understanding your target market’s needs will help determine the appropriate capacity for optimal operation. -
Power Supply
Pencil vending machines may be manually operated or require electrical power for features like digital displays or card payment systems. Identifying the power supply requirements is vital, particularly for international buyers, as voltage and plug type can vary by region. This ensures compatibility and minimizes installation issues. -
Dimensions and Weight
The size and weight of the vending machine can influence its placement and transportation costs. Compact machines may be ideal for limited spaces, while larger models may offer additional features. Buyers should assess the installation site and consider any shipping constraints when evaluating dimensions. -
User Interface
The design and functionality of the user interface are essential for customer satisfaction. Options include touch screens, buttons, or coin acceptors. A user-friendly interface can enhance the purchasing experience and reduce the likelihood of malfunctions, directly impacting sales. -
Security Features
Security is paramount in vending machine operations to prevent theft and vandalism. Features such as reinforced locks, tamper-proof designs, and surveillance capabilities can protect investments. Understanding the security measures in place can help buyers feel more confident in their purchase.
Common Trade Terminology
Familiarity with industry terminology can streamline communication and negotiations between buyers and suppliers. Here are some key terms to know:
-
OEM (Original Equipment Manufacturer)
This term refers to companies that produce components that are used in another company’s end product. In the context of pencil vending machines, an OEM may provide specific parts, ensuring compatibility and quality. Buyers should consider OEM relationships for reliable sourcing. -
MOQ (Minimum Order Quantity)
MOQ is the smallest quantity a supplier is willing to sell. Understanding MOQ is crucial for budget planning and inventory management. Buyers should negotiate MOQs that align with their sales forecasts to avoid excess inventory or supply shortages. -
RFQ (Request for Quotation)
An RFQ is a document sent to suppliers requesting price quotes for specific products or services. It is a critical step in the procurement process, allowing buyers to compare prices and terms from multiple vendors. A well-prepared RFQ can lead to better pricing and terms. -
Incoterms (International Commercial Terms)
These are standardized trade terms that define the responsibilities of buyers and sellers in international transactions. Familiarity with Incoterms such as FOB (Free On Board) and CIF (Cost, Insurance, and Freight) is essential for understanding shipping costs and liability during transit. -
Lead Time
This term refers to the time it takes from placing an order to receiving the product. Understanding lead times is vital for inventory management and planning. Buyers should inquire about lead times to ensure they can meet their market demands without disruption. -
Warranty
A warranty is a guarantee provided by the manufacturer regarding the repair or replacement of a product within a certain period. Understanding warranty terms is essential for assessing the long-term value of a pencil vending machine and planning for potential future costs.
By understanding these technical properties and trade terminologies, international B2B buyers can make well-informed decisions and foster successful procurement strategies in the pencil vending machine market.
Navigating Market Dynamics, Sourcing Trends, and Sustainability in the pencil vending machine Sector
Market Overview & Key Trends
The pencil vending machine sector is experiencing a notable shift driven by several global factors. Increasing urbanization and a growing emphasis on educational tools are propelling demand, particularly in emerging markets across Africa, South America, the Middle East, and Europe. As these regions invest in educational infrastructure, the need for accessible stationery solutions, including pencil vending machines, becomes paramount.
Technological advancements are also reshaping the market landscape. The integration of IoT technology into vending machines is enabling real-time inventory management and customer interaction, enhancing the user experience. International B2B buyers should be aware of these innovations, as they offer opportunities for improved operational efficiency and customer engagement. Additionally, there is a rising trend towards contactless payment systems, catering to a tech-savvy consumer base that prioritizes convenience and hygiene.
Sourcing trends are shifting towards local suppliers to mitigate supply chain disruptions and promote regional economic growth. For buyers in Africa and South America, establishing partnerships with local manufacturers can yield cost benefits and foster a sustainable procurement approach. Furthermore, as businesses increasingly prioritize agility, the demand for customizable vending solutions that can adapt to specific market needs is on the rise.
Sustainability & Ethical Sourcing in B2B
Sustainability is becoming a critical consideration in the pencil vending machine sector. The environmental impact of manufacturing processes and materials used in vending machines is under scrutiny, prompting buyers to seek eco-friendly options. Ethical sourcing is not only a regulatory requirement in many regions but also a key driver of consumer preference.
Buyers should prioritize vendors who utilize sustainable materials, such as recycled plastics and responsibly sourced wood for pencil production. Certifications such as FSC (Forest Stewardship Council) and ISO 14001 can serve as indicators of a supplier’s commitment to sustainability. Furthermore, implementing a circular economy model, where machines are designed for easy disassembly and recycling, can significantly reduce waste and enhance brand reputation.
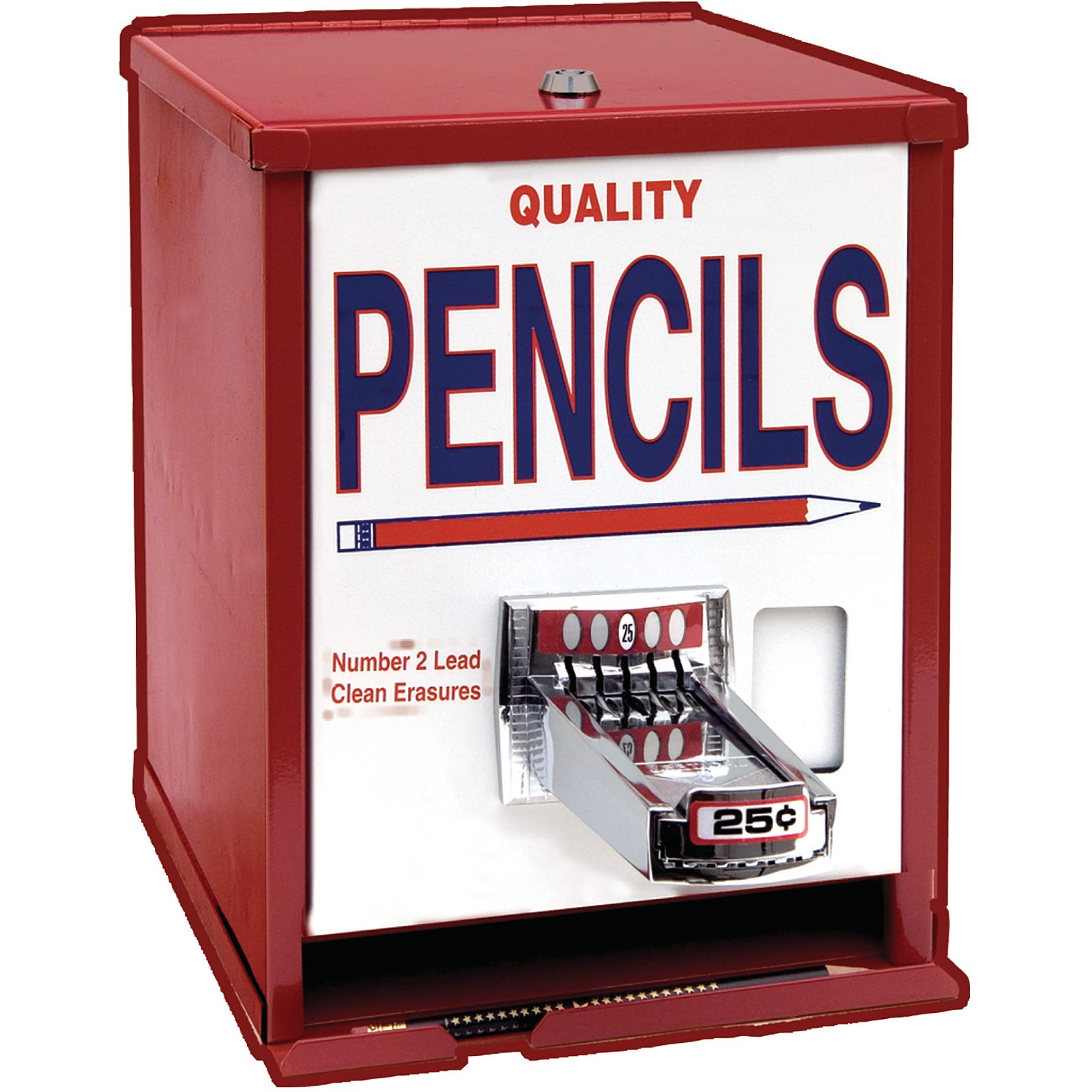
Illustrative Image (Source: Google Search)
By collaborating with suppliers that share a commitment to sustainable practices, international buyers can not only minimize their environmental footprint but also appeal to a growing demographic of environmentally conscious consumers. In regions like Europe, where sustainability standards are stringent, aligning with ethical suppliers can also enhance market competitiveness.
Brief Evolution/History
The pencil vending machine has evolved from simple mechanical designs to sophisticated automated units. Initially introduced in the early 20th century, these machines were primarily found in schools and offices, offering basic stationery supplies. Over the decades, technological advancements have transformed them into interactive vending solutions equipped with digital interfaces and cashless payment options.
The shift towards automation and digitalization reflects broader changes in consumer behavior and purchasing patterns. Today’s pencil vending machines not only dispense traditional stationery but also offer a variety of educational materials and tools, catering to diverse market needs. As the sector continues to innovate, understanding this evolution is essential for B2B buyers looking to capitalize on emerging trends and consumer preferences.
Related Video: International Trade Explained
Frequently Asked Questions (FAQs) for B2B Buyers of pencil vending machine
-
What criteria should I use to vet suppliers for pencil vending machines?
When vetting suppliers, prioritize their industry experience, production capacity, and reputation. Verify their credentials through references and reviews from previous clients, especially those in your region. Additionally, assess their certifications, such as ISO or CE, which can indicate adherence to quality standards. Request samples of their products to evaluate craftsmanship and functionality. Engaging in direct communication with potential suppliers can also provide insights into their customer service and responsiveness. -
Can I customize the design and features of the pencil vending machines?
Most manufacturers offer customization options, allowing you to tailor the vending machines to meet your specific needs. This can include branding with your logo, color schemes, and specific functionalities such as cashless payment systems or additional product offerings. Be clear about your requirements during initial discussions, and request detailed proposals that outline the customization process, associated costs, and timelines. Understanding the limits of customization can also help manage expectations. -
What are the typical minimum order quantities (MOQ) and lead times?
MOQs for pencil vending machines can vary significantly based on the supplier and the complexity of the order. Generally, MOQs can range from 10 to 100 units. Lead times also depend on the supplier’s production capabilities, but expect anywhere from 4 to 12 weeks after order confirmation. Always inquire about MOQs upfront to ensure they align with your purchasing plans, and confirm lead times to facilitate your project timelines and inventory management. -
What payment methods are commonly accepted, and what should I know about payment terms?
Suppliers typically accept various payment methods, including bank transfers, letters of credit, and online payment platforms. Familiarize yourself with the payment terms, as they can vary widely; some suppliers may require a deposit upfront with the balance due upon delivery, while others may offer flexible credit terms. Ensure that payment methods are secure and that you understand any fees involved. Establishing a clear payment agreement in advance can help prevent disputes later on. -
How can I ensure the quality of the pencil vending machines I order?
To ensure product quality, request detailed quality assurance (QA) protocols from your supplier. This should include information on testing procedures, materials used, and compliance with international standards. Consider conducting factory audits or hiring third-party inspection services to verify quality before shipment. Additionally, discuss warranty terms and after-sales support, as these can indicate the supplier’s confidence in their product quality. -
What certifications should I look for in a pencil vending machine supplier?
Look for suppliers that hold relevant certifications such as ISO 9001 for quality management and CE marking for compliance with European safety standards. These certifications demonstrate a commitment to quality and safety in manufacturing processes. Depending on your target market, other certifications may be beneficial, such as RoHS for environmental compliance. Request copies of these certifications and verify their validity to ensure compliance with local regulations. -
What logistics considerations should I keep in mind when importing vending machines?
Logistics plays a critical role in the procurement of pencil vending machines. Consider factors such as shipping methods, customs duties, and import regulations specific to your country. Engage a reliable freight forwarder who can manage the logistics process, including documentation and customs clearance. Understanding the total landed cost, which includes shipping, insurance, and taxes, is essential for budgeting. Plan for potential delays in transit and customs processing. -
How should I handle disputes with suppliers?
To mitigate disputes, establish clear communication channels and documented agreements at the outset of your relationship with suppliers. If a dispute arises, attempt to resolve it amicably through direct communication. Should that fail, refer to your contract for dispute resolution clauses, which may include mediation or arbitration. Maintaining a professional demeanor and focusing on mutual benefits can often lead to a satisfactory resolution. Keeping detailed records of all transactions and communications can also support your case if escalation is necessary.
Strategic Sourcing Conclusion and Outlook for pencil vending machine
In conclusion, the strategic sourcing of pencil vending machines presents a unique opportunity for international B2B buyers, particularly from regions like Africa, South America, the Middle East, and Europe. Key takeaways emphasize the importance of understanding local market dynamics, evaluating suppliers based on quality and reliability, and leveraging technology to streamline procurement processes.
By adopting a strategic sourcing approach, businesses can not only enhance operational efficiency but also ensure they are meeting the diverse needs of their customer base. The integration of innovative payment solutions and environmentally friendly materials in vending machines can further differentiate offerings in competitive markets.
Looking ahead, it is crucial for buyers to remain agile and responsive to emerging trends, such as the rise of e-commerce and the increasing demand for sustainable products. Engaging with suppliers who share a commitment to sustainability and innovation will be essential. As you consider your sourcing strategies, take proactive steps to explore partnerships that align with your business goals, ensuring your investment in pencil vending machines contributes to long-term success.